
Non-destructive Testing (NDE/NDT) Services: Pioneering Safety in Tower Inspections
Secure your investments and achieve unwavering confidence
From telecom masts to energy pipelines, our NDT methods set the gold standard for quality control, ensuring every tower stands tall and resilient against nature's tests.
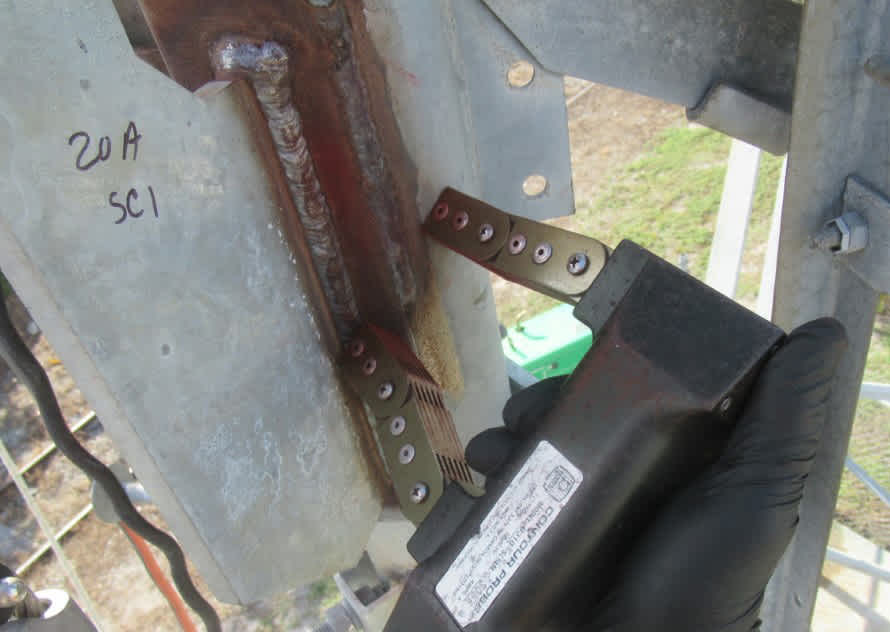
In the rapidly-evolving industries of telecom, construction, oil & gas, renewable energy, and fiber, the demand for reliability and safety has never been higher. As structures soar to unprecedented heights and dive deep beneath the earth, ensuring their integrity becomes paramount. Enter the realm of Non-destructive Testing (NDT) — the forefront of inspection innovation.
A Deep Dive into Non-destructive Testing
The essence of non-destructive testing lies in its ability to inspect, detect defects, and evaluate materials without causing any harm to the test object. From visual testing to advanced ultrasonic testing, NDT techniques ensure that both surface and subsurface defects are identified and addressed promptly.
Ultrasonic Testing
By leveraging high frequency sound waves, ultrasonic testing identifies defects within the internal and external surfaces. This method, including its advanced version, phased array ultrasonic testing, is a favorite for detecting flaws in welds, especially in the manufacturing processes of towering structures.
Magnetic Particle Testing and Inspection
A method tailored for ferromagnetic materials. The presence of a surface or slightly subsurface defect distorts the magnetic field, revealing the exact location of the flaw. Magnetic particle testing, with its magnetic particles, is a trusted technique for inspecting heavy-duty materials in the oil & gas sector.
Liquid Penetrant Testing
This method offers a keen eye for detecting surface defects, especially in non-porous materials. Liquid penetrant tests involve the application of a fluid on the test surface, which then seeps into any defects, marking them clear for inspection.
Radiographic Testing
Radiography non-destructive testing, harnessing the power of gamma rays, peers deep into materials to highlight both internal structure defects and external anomalies. It’s a vital method for pressure vessel evaluation and weld inspection.
Eddy Current and Electromagnetic Testing
Using electromagnetic fields, these testing methods identify defects in conductive materials. They're especially crucial in the aerospace and automotive sectors for fastener hole inspection and tube inspection.
Acoustic Emission and Vibration Analysis
These methods detect abrupt releases of energy in materials. Be it weld defects or corrosion, these techniques pick up the faintest of hints, ensuring nothing goes unnoticed.
While there are numerous other NDT methods, including laser testing, leak testing, and guided wave testing, the primary objective remains consistent: ensure the utmost quality and safety of materials without destructive means.
When it comes to the longevity and safety of towering structures, no stone should be left unturned. Trust our Non-destructive Testing (NDE/NDT) Services to be the guardian of your infrastructural ambitions. Dive into a world where quality meets safety, and innovation meets reliability.
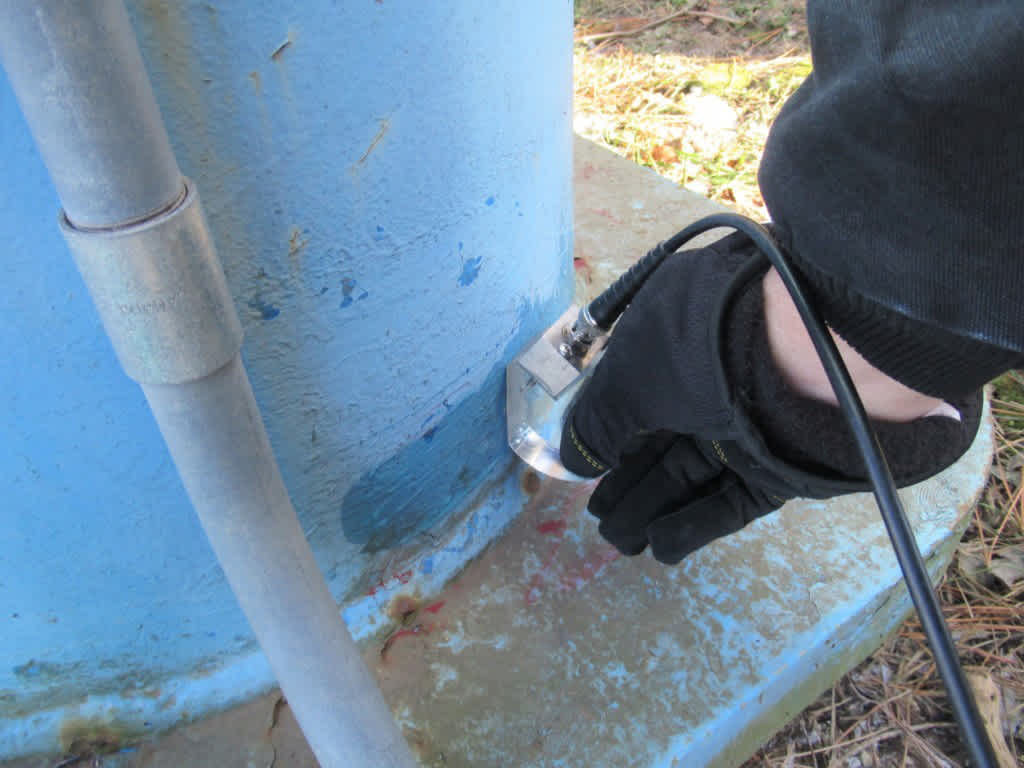
Value Delivered
Unparalleled Safety Assurance
With our non-destructive testing (NDT) services, ensure that your structures, be it in construction, telecom, or energy sectors, are devoid of any lurking defects that could compromise safety.
Cost-Efficiency
Detecting defects early with non-destructive inspection means reduced maintenance costs in the long run. Our testing methods ensure your investments are always protected.
Comprehensive Coverage
From surface inspection to deep subsurface defects, our diverse range of NDT techniques like visual inspections and eddy current testing provides holistic coverage.
Cutting-Edge Equipment
Our state-of-the-art testing equipment combined with seasoned maintenance professionals ensures precise results, every time.
Tailored Solutions
We understand that every project is unique. Thus, our NDT methods, from ultrasonic inspection to radiography testing, are customized to suit the specific needs of your industry.
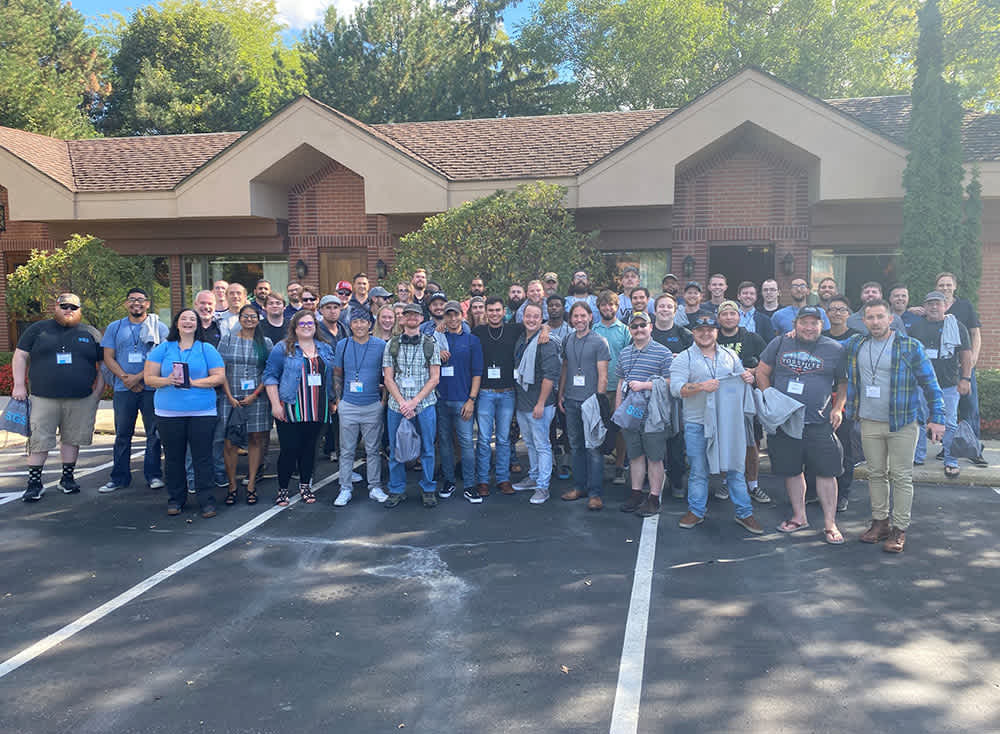
Pioneering Non-destructive Testing for Tower Integrity
SGS Corp's Non-Destructive Testing Services are at the forefront of ensuring tower material integrity, expertly detecting and evaluating defects to uphold the highest safety standards. Your assurance in every assessment.
From our clients
Wayne C., Texas Public Radio
Brian G., Pyramid Network Services, LLC
Frequently Asked Questions
The main purpose of NDT is to evaluate the properties of a material, component, or system without causing damage. It's a way to ensure safety and reliability without disrupting the integrity of the inspected item.
The choice of method depends on the material being tested, the type of defect anticipated, the equipment available, and the overall costs involved. For instance, magnetic particle testing is specific to ferromagnetic materials, while ultrasonic testing can be used for a broader range of materials.
While NDT is a subset of QC, not all QC methods are non-destructive. QC encompasses a broader range of activities, including destructive testing, that ensures a product meets specified criteria. NDT focuses only on testing methods that do not harm or destroy the material.
Yes. Every NDT method has its own set of limitations. For example, while ultrasonic testing can detect subsurface defects, it might be less effective on very thin materials or on materials with coarse grain structures.
Advanced Engineering and Inspection Solutions by SGS
Experience the pinnacle of engineering and inspection efficiency with SGS. Our expertly engineered solutions in building, maintaining, and upgrading your infrastructure promise unparalleled performance and reliability.